鋼鐵企業(yè)含鐵塵泥固廢的資源化利用
2017-07-03 作者:佚名 網(wǎng)友評論 0 條
隨著世界鋼鐵產(chǎn)量的大幅增長,鋼鐵企業(yè)內(nèi)部所產(chǎn)生的含鐵塵泥固廢物也日益增多,如無法合理有效的資源化,不僅會造成資源的浪費,還會嚴(yán)重污染環(huán)境。
李東海[1] ,鄭君[1],羅磊[1],倪曉明[2]
1.重慶賽迪熱工環(huán)保工程技術(shù)有限公司 2.中冶賽迪技術(shù)研究中心有限公司
1 前言
近十幾年來,隨著鋼鐵產(chǎn)量的迅猛發(fā)展,鋼鐵企業(yè)所產(chǎn)生的固廢也隨之與日俱增,帶來了巨大的環(huán)境和資源壓力,也制約著企業(yè)的進(jìn)一步發(fā)展。因此,在當(dāng)前環(huán)保要求與資源限制日趨加重的情況下,積極開發(fā)應(yīng)用新技術(shù)以資源化處置鋼鐵企業(yè)所產(chǎn)生的固廢具有十分重要的意義。
鋼鐵企業(yè)固廢是指在冶煉和加工過程中所產(chǎn)生的各類固體廢棄物,如冶煉渣(高爐渣和鋼渣等)、含鐵塵泥(包括原料、焦化、燒結(jié)、煉鐵、煉鋼及軋鋼單元收集的各類除塵灰泥)、廢鋼、廢耐火材料、部分危廢、以及其他垃圾、水處理污泥等等。一般總發(fā)生量約占鋼鐵企業(yè)產(chǎn)能的百分之六十(各企業(yè)因生產(chǎn)工藝技術(shù)不同會有所差異),而其中高爐渣及鋼渣占整個固廢量的三分之二左右,含鐵塵泥約占10%~20%,這也是鋼鐵企業(yè)主要面臨的兩大類固廢。
以中國某年產(chǎn)量1000萬噸規(guī)模的大型聯(lián)合鋼鐵企業(yè)為例,表1是其當(dāng)前固廢產(chǎn)生量及利用路徑的概況。其中,高爐渣和鋼渣經(jīng)再加工可用作水泥等建筑材料,已基本實現(xiàn)全量利用;含鐵塵泥主要以廠內(nèi)自循環(huán)為主、外銷為輔,由于含鐵塵泥中的鋅等易揮發(fā)元素在高爐內(nèi)會不斷循環(huán)富集,再加上廢鋼、低品位雜礦的不斷引入,導(dǎo)致除塵泥中的鋅含量不斷攀升,鋅負(fù)荷上升將直接導(dǎo)致高爐工況惡化,影響順行,爐喉結(jié)瘤,耐材侵蝕,壽命縮短,因此高爐需嚴(yán)格控制鋅入爐量,從而導(dǎo)致內(nèi)部自循環(huán)消化能力不斷降低,大量的高鋅含鐵塵泥只能暫時堆存或者外銷處理,不僅造成了資源的浪費,還會帶來二次污染,威脅生態(tài)環(huán)境。隨著當(dāng)下環(huán)保壓力的不斷加大,含鐵塵泥固廢的外銷轉(zhuǎn)移已愈發(fā)困難,如何有效利用含鐵塵泥固廢是亟待解決的嚴(yán)重問題。
表1 某年產(chǎn)量1000萬 t規(guī)模鋼鐵企業(yè)固廢產(chǎn)生量及利用路徑表(單位:×103t/a)
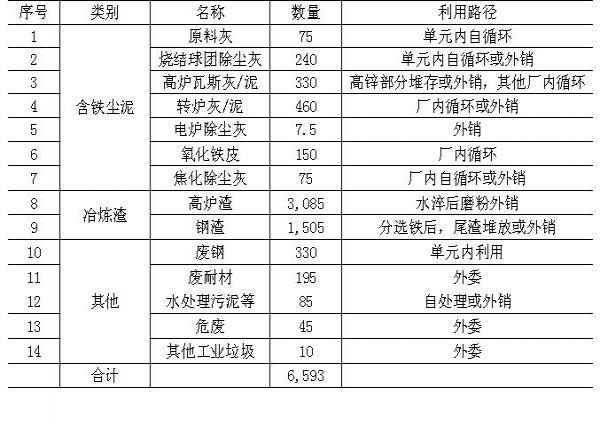
2 含鐵塵泥類固廢資源化利用技術(shù)
由于鋼鐵企業(yè)環(huán)節(jié)眾多,生產(chǎn)原料也差異較大,因此所產(chǎn)生固廢的物化特性也各有不同,須在少影響甚至不影響現(xiàn)行生產(chǎn)的前提下,綜合運用不同的技術(shù)路線,實現(xiàn)含鐵塵泥固廢的最優(yōu)化處置。為減少高爐內(nèi)有害元素鋅的富集,高爐瓦斯灰/泥、電爐灰等含鋅較高塵泥可通過轉(zhuǎn)底爐脫鋅處理后再返回使用;轉(zhuǎn)爐灰/泥等煉鋼塵泥可直接冷壓成球后作煉鋼冷卻劑,形成煉鋼系統(tǒng)內(nèi)部的短流程循環(huán)利用;無鋅和低鋅塵泥可作為含鐵原料混勻調(diào)質(zhì)后作為含鐵原料進(jìn)入燒結(jié)重新利用。
2.1 轉(zhuǎn)底爐技術(shù)
?。?)工藝流程
轉(zhuǎn)底爐屬煤基直接還原煉鐵技術(shù),其典型的工藝流程如圖2所示。將含鋅含鐵塵泥與粘結(jié)劑、還原劑按照一定比例混合均勻后,經(jīng)成型、干燥后送入轉(zhuǎn)底爐,在爐內(nèi)進(jìn)行高溫焙燒,大約30分鐘,物料內(nèi)部的碳元素將鐵、鋅氧化物快速還原,鋅在爐內(nèi)將變成蒸汽從球團(tuán)內(nèi)逸出,進(jìn)入煙氣系統(tǒng)再氧化后以氧化鋅形式被捕集回收,而鐵則主要以金屬單質(zhì)形態(tài)留存于球團(tuán)內(nèi)(即直接還原鐵DRI),經(jīng)冷卻后供高爐、轉(zhuǎn)爐使用。一條年處理塵泥20萬t的轉(zhuǎn)底爐處理線,可生產(chǎn)金屬化球團(tuán)~13萬t,粗鋅粉~4000t。實現(xiàn)金屬化率≥70%,脫鋅率≥80%。
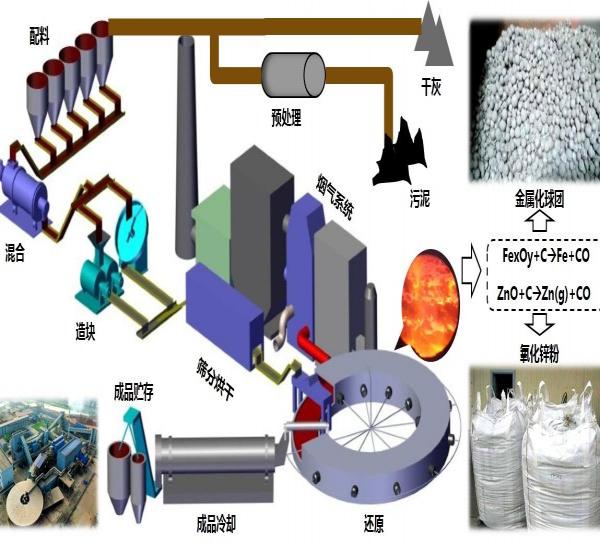
圖1 轉(zhuǎn)底爐工藝流程簡圖
?。?)關(guān)鍵技術(shù)
1)塵泥成型技術(shù)
由于各廠生產(chǎn)所用原料和工藝的不同,轉(zhuǎn)底爐所處理物料的物化性質(zhì)差異往往較大,物料的粒度大小、親水性、粘黏性、成球性也各有不同。目前主要的成型技術(shù)有圓盤造球和對輥壓塊兩種:圓盤成球適用于粒度細(xì)小、親水性好、易成球的粉塵,其產(chǎn)量與質(zhì)量波動較大;對輥壓塊對于原料的適應(yīng)性較強(qiáng),生球強(qiáng)度高,產(chǎn)量與質(zhì)量較穩(wěn)定,其使用粘結(jié)劑及運行成本相對較高。兩種成型技術(shù)需依據(jù)企業(yè)實際情況,根據(jù)塵泥特點,因地制宜地選擇與之相匹配的成型技術(shù)。
2)含碳球團(tuán)自還原控制技術(shù)
含碳球團(tuán)在爐內(nèi)的停留時間通常只有20~30分鐘,生產(chǎn)周期很短,但其過程卻十分復(fù)雜,涉及煤氣燃燒及氣體流動、含碳球團(tuán)的自還原和氣固兩相的傳熱傳質(zhì)等,各過程相互影響與耦合,而且由于工藝流程較長,生產(chǎn)調(diào)節(jié)反饋的滯后性大,控制難度高。傳統(tǒng)的控制手段各單元孤立而無關(guān)聯(lián),基本只能靠人工長期摸索積累經(jīng)驗,難以滿足轉(zhuǎn)底爐全線生產(chǎn)的智能控制需求。因此,立足工業(yè)生產(chǎn)的大數(shù)據(jù)分析,構(gòu)建起關(guān)鍵工藝參數(shù)、生產(chǎn)操作制度與產(chǎn)品質(zhì)量之間的專家系統(tǒng),是實現(xiàn)轉(zhuǎn)底爐內(nèi)含碳球團(tuán)自還原精準(zhǔn)控制技術(shù)的關(guān)鍵。
3)煙氣余熱及鋅粉回收技術(shù)
轉(zhuǎn)底爐熱效率較低,煙氣會帶走爐內(nèi)大量的熱量,與此同時,煙氣中還含有產(chǎn)品鋅粉,因此需配套余熱鍋爐及收粉布袋除塵器對煙氣中的余熱和鋅粉進(jìn)行回收。然而,由于轉(zhuǎn)底爐所處理的冶金含鋅塵泥還伴有K、Na、Pb、Cl等多種揮發(fā)性元素,進(jìn)入煙氣后極易引起鍋爐管束、收粉布袋的堵塞及腐蝕,嚴(yán)重制約生產(chǎn)順行。所以,高效防粘堵的余熱回收及凈化技術(shù)至關(guān)重要!合理控制煙氣的溫降,設(shè)置多級組合清灰措施,從而實現(xiàn)鍋爐及收粉系統(tǒng)的順行。
4)關(guān)鍵裝備設(shè)計
轉(zhuǎn)底爐工藝由于原料復(fù)雜,工況惡劣,需對相應(yīng)的轉(zhuǎn)底爐布料、爐體、出料螺旋、冷卻裝置等核心裝備進(jìn)行針對性的適應(yīng)性設(shè)計,實現(xiàn)系統(tǒng)的穩(wěn)定、長壽、高效作業(yè)。
2.2 冷壓塊技術(shù)
冷壓塊技術(shù)是指塵泥與粘結(jié)劑混合后使用壓球機(jī)擠壓成型,經(jīng)烘干或養(yǎng)護(hù)等方法以獲得高強(qiáng)度冷固球團(tuán),主要用于處理煉鋼系統(tǒng)產(chǎn)生的除塵灰(泥)、氧化鐵皮等,產(chǎn)品可直接回到轉(zhuǎn)爐作冷卻劑和造渣劑。該技術(shù)作為一種塵泥短流程回用技術(shù),具有投資少、流程短、生產(chǎn)靈活等特點。
……
相關(guān)文章
[錯誤報告] [推薦] [收藏] [打印] [關(guān)閉] [返回頂部]