HIsmelt工藝冶煉釩鈦磁鐵礦工業(yè)試驗(yàn)
2021-10-21 作者:佚名 網(wǎng)友評(píng)論 0 條
曹朝真1,2,張函冠3,王金霞4,張笑然3,
陳慶恒3,王林順4,李成峰3,張冠琪4
1.北京首鋼國(guó)際工程技術(shù)有限公司2.北京市冶金三維仿真設(shè)計(jì)工程技術(shù)研究中心
3. 承德信通首承科技有限責(zé)任公司4. 山東墨龍石油機(jī)械股份有限公司
釩鈦磁鐵礦是一種典型的多金屬伴生礦,具有極高的綜合利用價(jià)值,但由于其貧、細(xì)、散、雜的特殊性,給其冶煉帶來了一定困難,目前,對(duì)于釩鈦磁鐵礦的冶煉主要以高爐流程為主。在高爐冶煉釩鈦礦生產(chǎn)過程中,在高爐內(nèi)的高還原勢(shì)和高溫條件下,鈦的氧化物會(huì)被部分還原并生成高熔點(diǎn)的TiN和TiC,這些高熔點(diǎn)的物質(zhì)會(huì)引起爐渣變稠,嚴(yán)重時(shí)造成出渣和渣鐵分離困難;此外,由于還原反應(yīng)生成更多氣體以及釩鈦渣的發(fā)泡特性,造成高爐冶煉釩鈦礦易出現(xiàn)泡沫渣,使高爐下部透氣性惡化,從而影響正常生產(chǎn)[1-3]。
與高爐工藝不同,HIsmelt工藝爐內(nèi)沒有固體料柱,同時(shí)由于采用較高的二次燃燒率,使得SRV爐內(nèi)熔渣的氧勢(shì)與高爐相比顯著提高,這一根本性的技術(shù)特征使得HIsmelt工藝在冶煉釩鈦礦時(shí),渣中的TiO2不會(huì)被過度還原形成高熔點(diǎn)物質(zhì),從而使得爐渣能夠保持較好的流動(dòng)性,有利于冶煉過程的穩(wěn)定進(jìn)行。國(guó)內(nèi)首座年產(chǎn)80萬噸鐵水的墨龍HIsmelt工廠已于2016年建成投產(chǎn)[4],通過4年多的工業(yè)生產(chǎn)實(shí)踐和工藝改進(jìn),各項(xiàng)技術(shù)經(jīng)濟(jì)指標(biāo)和運(yùn)行穩(wěn)定性顯著提高[5],為開展HIsmelt工業(yè)試驗(yàn)奠定了基礎(chǔ)。以首承釩鈦礦為原料,在墨龍HIsmelt熔融還原爐上進(jìn)行了首次100%釩鈦磁鐵礦冶煉工業(yè)試驗(yàn),研究了SRV爐冶煉釩鈦磁鐵礦適宜的工藝參數(shù)和冶煉規(guī)律,為HIsmelt工藝冶煉釩鈦礦進(jìn)行了工業(yè)化探索。
1試驗(yàn)原料
本次試驗(yàn)以首承釩鈦磁鐵礦氧化球團(tuán)為原料,經(jīng)破碎后獲得6mm以下粉料,用作SRV爐噴吹含鐵原料,含鐵粉料的粒度原則應(yīng)滿足-0.1mm<10%和+4mm<10%。試驗(yàn)配礦用鐵礦粉采用PB粉,噴吹煤和熔劑均采用墨龍現(xiàn)場(chǎng)原料。首承釩鈦磁鐵礦和PB粉主要化學(xué)成分見表1。
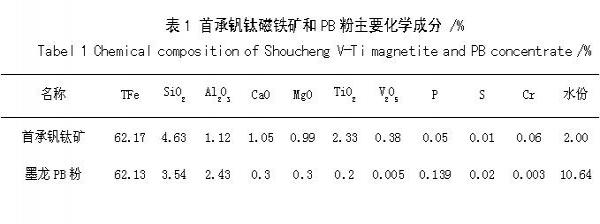
由表1可以看到,首承釩鈦球粉TiO2含量相對(duì)較低為2.33%,屬于低鈦型釩鈦磁鐵礦,S和P含量較低,Cr含量偏高。
2試驗(yàn)方法
試驗(yàn)分階段進(jìn)行,釩鈦磁鐵礦的初始配入量為40%,爐內(nèi)物料置換完全后,按照60%、80%、100%依次增加釩鈦礦配比。試驗(yàn)初始階段,爐渣二元堿度控制在1.1-1.25,Mg/Al=0.5-0.6,試驗(yàn)過程中,根據(jù)渣鐵成份、泡沫渣、爐內(nèi)燃燒、爐體熱負(fù)荷、煤氣成份及溫度波動(dòng)等情況,判斷是否進(jìn)入下一階段。試驗(yàn)期間取渣樣、鐵樣和煤氣灰樣進(jìn)行快速分析,并做好記錄。試驗(yàn)選取臨近日期且SRV爐平穩(wěn)運(yùn)行的生產(chǎn)數(shù)據(jù)作為基準(zhǔn)期數(shù)據(jù)。
3試驗(yàn)結(jié)果及分析
3.1試驗(yàn)過程及結(jié)果
本次試驗(yàn)過程共分為四個(gè)階段,具體過程見表2。
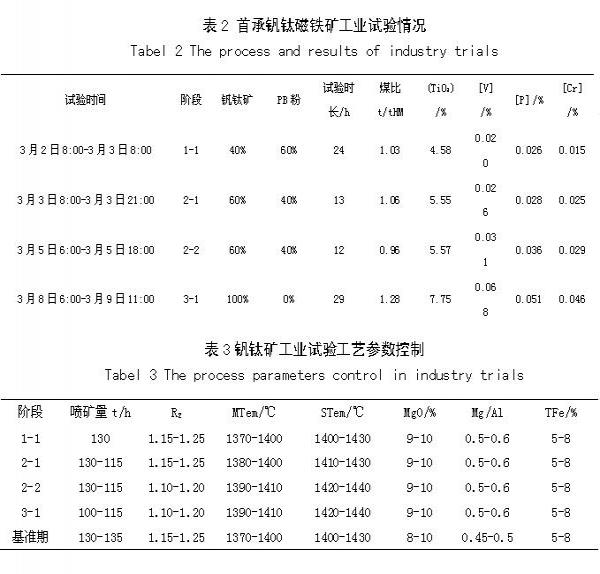
1-1階段試驗(yàn)從3月2日8:00開始至3月3日8:00結(jié)束,冶煉過程中,固定釩鈦礦配比為40%,噴煤量為69.5t/h,R2=1.2,渣中MgO=9-10%,熱風(fēng)量為15萬Nm3/h,初始噴礦量為130t/h,通過調(diào)節(jié)噴礦量來調(diào)節(jié)爐況。試驗(yàn)過程中,爐況整體情況穩(wěn)定,冶煉正常。渣中FeO%偏高約為10%,渣中TiO2%最高達(dá)到3.8%,渣中V2O5%最高為0.38%;試驗(yàn)過程中為維持合理的二次燃燒率,噴礦量由130t/h逐步降低至115t/h,受噴礦量減少影響,爐渣溫度穩(wěn)步由1410℃升高至1440℃, 煤氣熱值有所升高。鐵水溫度基本控制在1380-1400℃,鐵水C%由4.0%左右升至4.1%;出渣情況良好,渣量大,流動(dòng)性好。
2-1階段試驗(yàn)從3月3日8:00開始至3月3日21:00結(jié)束,在1-1階段試驗(yàn)的基礎(chǔ)上,釩鈦礦配比提高至60%,其他條件不變。試驗(yàn)過程中,根據(jù)爐內(nèi)情況噴礦量迅速由130t/h降為115t/h,渣中FeO%維持在10%左右,渣中TiO2%最高至5.55%,渣中V2O5%升高至0.45%,爐渣溫度進(jìn)一步由1440℃升高至1460℃,鐵水溫度有所降低,控制在1370-1380℃,鐵水C%由4.1%最高升至4.18%;鐵水中Cr%、V%逐步升高,60%釩鈦礦物料入爐3小時(shí)開始,爐渣出現(xiàn)泡沫渣跡象。
2-2階段試驗(yàn)從3月5日6:00開始至3月5日18:00結(jié)束,鑒于2-1階段試驗(yàn)后期出現(xiàn)泡沫渣現(xiàn)象,在恢復(fù)爐況后,重新開始釩鈦礦配比60%試驗(yàn),初始噴礦量為130t/h,其他條件不變。本階段試驗(yàn)過程與2-1階段情況相似,渣中FeO前期逐步升高,降礦后,明顯降低至8.6%,渣中TiO2%最高至5.57%,渣中V2O5%升高至0.4%,釩鈦礦入爐一段時(shí)間后,煤氣熱值逐步提升,二次燃燒率開始逐步降低,為維持合理爐況,噴礦量由130t/h逐步降低至115t/h,試驗(yàn)過程中,渣量大,并始終具有較好的流動(dòng)性,出現(xiàn)較明顯泡沫渣。
3-1階段試驗(yàn)從3月8日6:00開始至3月9日11:00結(jié)束,為了降低泡沫渣的影響,本階段試驗(yàn)初始噴礦量固定為100t/h,釩鈦礦配比固定為100%,同時(shí)噴煤量和熱風(fēng)量均相應(yīng)下調(diào)。100%釩鈦礦物料入爐后,渣中FeO%逐步升至10.2%,后降低至7-8%并保持平穩(wěn),提高噴礦量后有所提高,渣中TiO2%最高至7.75%,渣中V2O5%升高至0.55%,Ti和V在渣和鐵水間的分配系數(shù)分別為492和5.3;出渣過程基本正常,未出現(xiàn)明顯泡沫渣,逐步提高噴礦量至115t/h后,爐況波動(dòng)有所加劇,有少量泡沫渣,但在可控范圍內(nèi)。
3.2試驗(yàn)結(jié)果分析
3.2.1爐渣FeO含量升高原因分析
本次工業(yè)試驗(yàn)結(jié)果表明,全釩鈦礦冶煉時(shí)渣中FeO含量約為7-9%,與普通礦冶煉相比約升高2-3個(gè)百分點(diǎn)。由于試驗(yàn)過程中使用的噴吹煤及其它原料與冶煉普通礦時(shí)相同,而且試驗(yàn)時(shí)噸鐵噴煤量較普通礦冶煉時(shí)有所提高,因此造成渣中FeO含量升高的原因應(yīng)與釩鈦礦本身的特性有關(guān)。
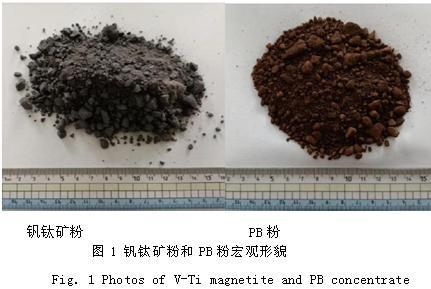
對(duì)兩種礦粉的粒度分布進(jìn)行了對(duì)比。由圖1可以看出,釩鈦礦粉呈深灰色,半球顆粒中摻雜部分細(xì)粉,與PB粉相比,目測(cè)其大顆粒和超細(xì)粉占比偏多。為此對(duì)上述兩種礦粉的粒度進(jìn)行爐檢測(cè),結(jié)果見圖2。
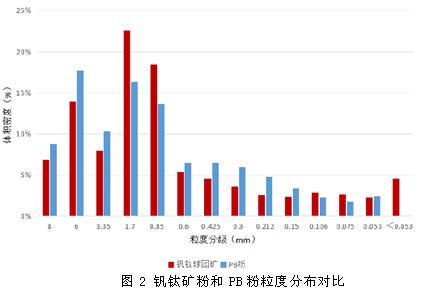
Fig. 2 Comparison of particle size distribution between V-Ti magnetite and PB concentrate
由圖2可以看出,粒徑≥0.85mm的礦粉顆粒占比中,釩鈦礦粉要明顯高于PB粉,而粒徑在0.85mm以下的礦粉顆粒占比則相反,可見,整體上釩鈦礦粉的平均粒徑要大于PB粉。礦粉粒度增大會(huì)延長(zhǎng)礦粉在爐內(nèi)的還原時(shí)間,導(dǎo)致渣中FeO含量有所升高。除此之外,礦粉的還原性差異也會(huì)對(duì)渣中FeO含量帶來顯著影響。
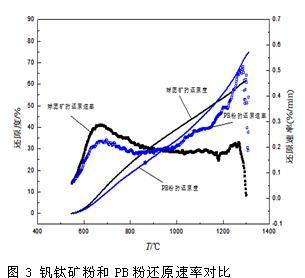
Fig. 3 Comparison of reduction rate between V-Ti magnetite and PB concentrate
圖3為釩鈦礦粉和PB粉煤粉還原實(shí)驗(yàn)結(jié)果對(duì)比圖。從實(shí)驗(yàn)結(jié)果可知,在900℃以下,釩鈦礦粉的還原速率略高于PB粉,二者差別不大;隨著反應(yīng)溫度的升高,釩鈦礦粉的還原速度呈緩慢降低的趨勢(shì),在900℃至1200℃區(qū)間內(nèi),還原速率基本保持不變,PB粉的還原速率在1000℃以上迅速升高,且遠(yuǎn)大于釩鈦礦粉。對(duì)比認(rèn)為,釩鈦礦粉還原性差是造成渣中FeO含量的主要原因之一。
3.2.2爐渣特性分析
表4為全釩鈦礦冶煉時(shí)水渣的主要化學(xué)成份,渣中TiO2含量為7.08,屬于低鈦渣。
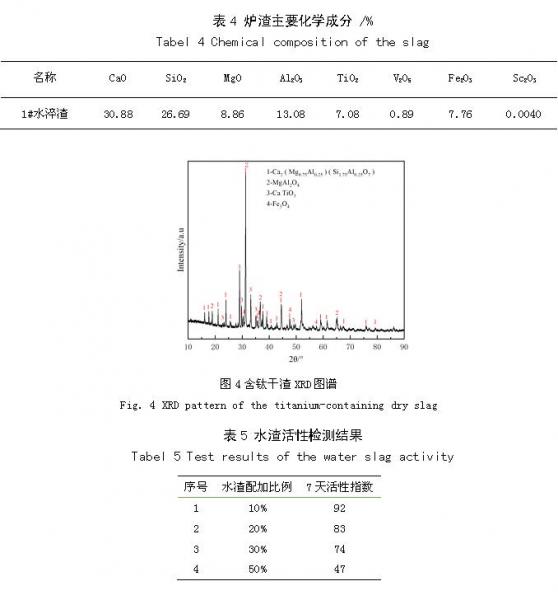
圖4為全釩鈦礦冶煉時(shí)SRV爐干渣的XRD圖譜,從圖中可以看出,爐渣干渣物相成份主要以Ca2(Mg0.75Al0.25)(Si1.75Al0.25O7)、MgAl2O4、CaTiO3、Fe3O4等為主,其中TiO2主要以鈣鈦礦形式存在。傳統(tǒng)的高爐水渣是重要的礦渣水泥原料,渣中TiO2含量增加會(huì)對(duì)爐渣活性帶來不利影響,為了檢測(cè)全釩鈦礦冶煉時(shí),含鈦水渣的活性,對(duì)不同含鈦水渣配比的水泥活性進(jìn)行了檢測(cè)。從表5檢測(cè)結(jié)果可以看出,隨著水渣配比升高,水泥7天活性指數(shù)顯著降低,水渣配比為50%時(shí),水泥7天活性指數(shù)為47,按照不同標(biāo)號(hào)水泥對(duì)活性指數(shù)的要求,含鈦SRV水渣在實(shí)際使用時(shí)其配加量相較于普通高爐渣會(huì)有所降低。
3.2.3釩、鈦在渣鐵間分配規(guī)律
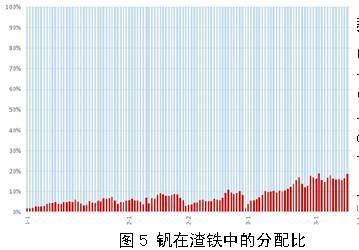
Fig. 5 Distribution ratio of V between slag and hot metal
圖5為試驗(yàn)期間各階段釩在渣鐵中的分配比變化圖。由圖中可知,隨著釩鈦礦粉配入量的增加,進(jìn)入鐵水中的釩的比例逐步升高,全釩鈦礦冶煉時(shí),釩在渣鐵中的分配比約為5.3,與1-1階段相比,降低約72%。釩在渣鐵中分配比的提高與煤比增加有關(guān),過量的煤粉使得爐內(nèi)的還原勢(shì)相對(duì)增強(qiáng),從而使更多的釩被還原進(jìn)入鐵水。
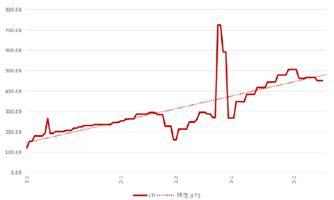
圖6 鈦在渣鐵中的分配比
Fig. 6 Distribution ratio of Ti between slag and hot metal
圖6為試驗(yàn)期間各階段鈦在渣鐵中的分配比變化圖。試驗(yàn)期間,隨著釩鈦礦粉配入量的增加,(Ti)含量逐步升高,但[Ti]含量相對(duì)穩(wěn)定,全釩鈦礦冶煉時(shí),鈦在渣鐵中的分配比約為492。
3.2.4泡沫渣的生成原因分析
……
關(guān)注“driinfo",手機(jī)上同步看直接還原、鋼鐵業(yè)內(nèi)文章
相關(guān)文章
[錯(cuò)誤報(bào)告] [推薦] [收藏] [打印] [關(guān)閉] [返回頂部]