菱鐵礦煤基直接還原聯(lián)產(chǎn)DRI和活性炭的研究
2021-02-24 作者:佚名 網(wǎng)友評論 0 條
朱德慶,潘建,郭正啟*,楊聰聰,薛鈺霄,石玥,段真,王毅格
中南大學(xué)資源加工與生物工程學(xué)院
我國菱鐵礦資源豐富,探明儲量為18.34億t,但其“貧、細(xì)、雜”的特點,造成常規(guī)選礦方法無法使之有效分選,目前其開采量不足總儲量的10%[1-4]。同時,由于其鐵品位低、燒損大,在常規(guī)燒結(jié)球團(tuán)工藝中,其產(chǎn)品強度差,設(shè)備生產(chǎn)能力低,燃料消耗也因碳酸鹽分解而增加,很難大配比直接利用[6-8]。目前,磁化焙燒-弱磁選工藝是處理菱鐵礦的主流工藝,但存在能耗高的問題[9-11]。直接還原—磁選技術(shù)是近些年發(fā)展起來能夠有效處理復(fù)雜含鐵資源的新技術(shù)。
另一方面,活性炭用于煙氣同時脫硫脫硝作為一種能協(xié)同多污染物同時治理的技術(shù),在高效脫除SO2及NO的同時,還能脫除煙氣中的粉塵、重金屬、二噁英等污染物,目前被認(rèn)為是一種極具發(fā)展前景的煙氣脫硫脫硝技術(shù)。但由于目前的活性炭生產(chǎn)流程長,設(shè)備操作、運行維修較復(fù)雜,造成活性炭價格昂貴(市售脫硫脫硝活性炭價格4000~5000元/噸),鋼鐵廠用活性炭法脫硫脫硝運行成本達(dá)到15~22元/噸,按全國年產(chǎn)燒結(jié)礦10億噸計,鋼鐵企業(yè)僅燒結(jié)煙氣脫硫脫硝的運行費用就達(dá)150~220億元,且活化過程中存在二次污染,嚴(yán)重制約著該技術(shù)的推廣應(yīng)用?;钚蕴績r格居高不下主要由于生產(chǎn)過程中最主要的兩個環(huán)節(jié)炭化和活化分步進(jìn)行,造成設(shè)備投資、運行成本,占地面積及能源消耗高。從上世紀(jì)末開始就有學(xué)者考慮將炭化和活化合并為一步,使用一步法制備活性炭,從而降低設(shè)備投資、運行成本,及活性炭價格,并取得了一定的進(jìn)展。但目前關(guān)于一步法制備活性炭技術(shù)研究仍主要集中在用化學(xué)試劑浸漬進(jìn)行同時炭化活化,而該技術(shù)活化劑難回收、活性炭再生工藝復(fù)雜,且易造成二次污染。而關(guān)于物理活化一步法方面雖然也取得了一定的進(jìn)展,證明該技術(shù)可以制備孔徑發(fā)達(dá),吸附性能較好的活性炭,但國內(nèi)外關(guān)于此方面的文獻(xiàn)報導(dǎo)和研究仍較少,近年來鮮有報道。
本論文提出一種基于直接還原工藝的一步法活性炭制備技術(shù),即以我國資源豐富、價格低廉、來源廣泛的高揮發(fā)性的低階煤(煙煤、褐煤)為基炭,以菱鐵礦分解產(chǎn)生的鐵氧化物為添加劑,利用低階煤熱解和氣化反應(yīng)及菱鐵礦分解和直接還原鏈?zhǔn)椒磻?yīng)之間的耦合,一步實現(xiàn)煤的炭化和活性炭基體的活化,同步產(chǎn)出菱鐵礦直接還原鐵粉和活性炭,無三廢產(chǎn)生。該工藝可以一步實現(xiàn)低階煤到活性炭的提質(zhì),同時實現(xiàn)復(fù)雜菱鐵礦資源的高效利用,縮短工藝流程、無廢水和廢渣排放,生產(chǎn)過程無需額外的活化劑(如CO2和水或酸、堿等化學(xué)試劑),制備出的直接還原鐵粉可作為電爐煉鋼優(yōu)質(zhì)原料,資源得到高效利用,并產(chǎn)生直接經(jīng)濟效益,因而可顯著降低活性炭生產(chǎn)成本,符合活性炭高效清潔低成本生產(chǎn)及短流程煉鋼的發(fā)展趨勢。
1 原料性能及研究方法
1.1 原料性能
各原料化學(xué)成分見表1,低階煤工業(yè)分析見表2。菱鐵礦鐵品位較低,僅35.43%,脈石含量高,SiO2含量高達(dá)10.75%,CaO含量為4.91%,有害元素磷含量較低,但硫含量較高,為0.24%,其屬碳酸鹽類,燒損大,LOI為28.89%。此外,研究表明[18],回轉(zhuǎn)窯直接還原用對還原煤的要求一般為固定碳FCad含量宜在50%以上,揮發(fā)分Vad在30%左右,灰分Aad含量越低越好,最好小于10%,全硫含量在1%以下,焦渣特征數(shù)值不高于2。因此,低階煤適合作直接還原用煤。另一方面,在回轉(zhuǎn)窯溫度條件下達(dá)到平衡時,還原煤中的硫在高溫分解揮發(fā)后,生成的氣態(tài)硫化物(CS2、COS、H2S)和單質(zhì)硫(S2)容易被新生的固態(tài)鐵相吸收,尤其是新生金屬鐵的吸硫能力很強,因此有必要加入一定比例的脫硫劑[12, 13]。本文所用脫硫劑CaO含量為51.83%,燒損LOI為40.04%。各原料粒度組成見表3。
表1 原料化學(xué)成分(質(zhì)量分?jǐn)?shù)-%)
Table 1 Chemical compositions of raw materials (wt-%)
礦種 |
TFe |
SiO2 |
Al2O3 |
MgO |
CaO |
S |
P |
LOI |
菱鐵礦 |
35.43 |
10.75 |
2.66 |
1.38 |
4.91 |
0.240 |
0.033 |
28.89 |
低階煤SF |
23.86 |
27.62 |
8.02 |
1.34 |
24.94 |
5.170 |
0.010 |
95.51 |
脫硫劑 |
0.00 |
3.74 |
0.48 |
0.20 |
51.83 |
0.039 |
0.048 |
40.04 |
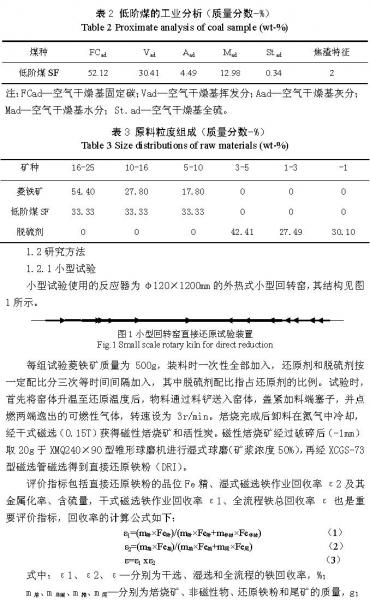
Fe焙、Fe非磁、Fe精、Fe尾—分別為焙燒礦、非磁性物、還原鐵粉和尾礦的全鐵質(zhì)量百分含量,%。
1.2.2擴大試驗
擴大試驗裝備采用中南大學(xué)自主研發(fā)的間歇式回轉(zhuǎn)窯,規(guī)格尺寸為Ø1000×500 mm。該回轉(zhuǎn)窯由供熱系統(tǒng)、加煤系統(tǒng)、排煙系統(tǒng)和窯體四部分組成。試驗操作制度為:首先待窯內(nèi)溫度達(dá)到目標(biāo)焙燒溫度后停窯,從加料口快速加入20~30Kg菱鐵礦和部分還原煤,加料后升溫至目標(biāo)溫度所需時間約為40min,然后開始恒溫計時。加料后開始陸續(xù)加入剩余還原煤,時間間隔大約10min。加入還原煤的量應(yīng)按預(yù)定的C/Fe質(zhì)量比進(jìn)行計算,所需還原煤在焙燒時間內(nèi)分15次左右加入,升溫過程加入三分之一的還原煤,恒溫過程加入三分之二的還原煤?;剞D(zhuǎn)窯轉(zhuǎn)速設(shè)為1.0rpm。還原過程中,通過調(diào)節(jié)空氣與天然氣比值來控制升溫速度,通過調(diào)節(jié)螺旋加煤機轉(zhuǎn)速控制加煤速度。還原結(jié)束后,關(guān)閉燒嘴和風(fēng)機,停窯,快速將焙燒礦卸入通氮氣的冷卻罐中,加蓋密封,外通水冷卻。冷卻后破碎至-10mm進(jìn)行干式磁選,磁場強度0.15T,干選磁性粗精礦破碎至-1mm后采用錐形球磨機進(jìn)行球磨,每次200g,濕式磁選采用CRIMM DC SF Φ400-300型筒式磁選機。干選所得非磁性物經(jīng)過篩分后,即為活性炭,然后進(jìn)行表征和分析。
1.2.3活性炭性能表征
本文對直接還原制備出的活性炭的碘吸附值、活性炭比表面積及孔徑分布進(jìn)行分析,分析方法見文獻(xiàn)。
本文采用靜態(tài)吸附法對活性炭的脫硫脫硝性能進(jìn)行評價。實驗裝置如圖2所示,實驗中保持一定空速和煙氣溫度,煙氣中SO2及NO濃度通過配氣進(jìn)行控制。實驗開始時,將一定量的活性炭加入反應(yīng)器中,打開加熱爐升溫至一定溫度后,通過靜態(tài)配氣法,調(diào)節(jié)各氣體流量,得到所需混合氣體,氣體經(jīng)混合器混合均勻后,經(jīng)過加熱爐加熱至一定溫度后,進(jìn)入反應(yīng)器并與活性炭層充分接觸,發(fā)生吸附,同時使用MGA5紅外煙氣分析儀對出口煙氣中各氣體濃度進(jìn)行實時檢測,當(dāng)出口SO2及NO濃度為入口處的80%時,結(jié)束實驗。全程吸附所用時間定義為穿透時間,吸附量定義為穿透容量。
通過對吸附全過程的SO2及NO進(jìn)行積分計算,可計算得到活性炭的穿透硫容量及穿透氮容量,其計算公式如2-6、2-7所示。
2 試驗結(jié)果與分析
2.1 小型試驗
2.1.1還原溫度及時間
在還原時間140min,C/Fe質(zhì)量比2.25,球磨細(xì)度-0.074mm占83.14%,濕式磁選磁場強度1000Gs的條件下,考查還原溫度對還原及濕式磁選的影響,結(jié)果如圖3所示。隨著還原焙燒溫度由950℃提高到1050℃,焙燒礦金屬化率逐漸升高,當(dāng)溫度高于1050℃后,金屬化率變化不大。磁選鐵精礦品位和鐵回收率在1050℃時達(dá)到最大值,分別為91.83%和94.68%。
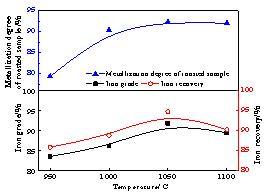
圖3 焙燒溫度對直接還原及磁選的影響
Fig.3 Effects of reduction temperature on reduction and magnetic separation
在還原溫度1050℃,C/Fe質(zhì)量比2.25,磨礦細(xì)度-0.075mm占83.14%,濕式磁選場強1000Gs的條件下,考查還原時間對直接還原及磁選指標(biāo)的影響,如圖4所示。在還原時間80-140min內(nèi),焙燒礦金屬化率緩慢增加,磁選指標(biāo)變化不大,磁選精礦鐵品位由89.79%上升至91.83%,鐵作業(yè)回收率在120min時達(dá)到最大,為95.07%。這主要因為菱鐵礦塊礦粒度較大,存在傳熱效應(yīng),內(nèi)層的還原速率低于外層。在還原末期,內(nèi)層的浮氏體和鐵橄欖石部分被還原的金屬鐵包裹,導(dǎo)致還原氣體擴散阻力增加,還原速率下降。因此,在還原120min后,還原指標(biāo)變化并不明顯。此外,在實際生產(chǎn)中,焙燒時間過長導(dǎo)致能耗高,利用系數(shù)下降,因此,該工藝適宜的還原焙燒時間為120-140min。
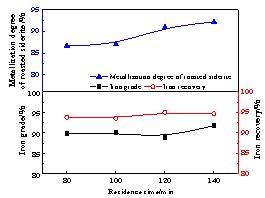
圖4焙燒時間對直接還原及磁選的影響
Fig.4 Effects of reduction duration on reduction and magnetic separation
2.1.2 C/Fe質(zhì)量比及脫硫劑用量
固定還原溫度1050℃,還原時間140min,磨礦細(xì)度-0.075mm占83.14%,濕式場強1000Gs,考查C/Fe比對還原及磁選的影響,如圖5所示。隨著C/Fe比由1.12提高到2.25,焙燒礦金屬化率逐漸增加,C/Fe比在1.86時金屬化率達(dá)到90%以上,鐵品位基本不變,回收率由91.92%增加至94.68%。對比常規(guī)的鐵礦球團(tuán)直接還原(一般C/Fe質(zhì)量比為0.6左右),從生產(chǎn)直接還原鐵的角度來看,C/Fe比為1.12已然足夠,但從煤提質(zhì)生產(chǎn)活性炭來看,配煤量應(yīng)適宜提高。當(dāng)然,C/Fe質(zhì)量比不能盲目無限制增加,不適宜的超量的配煤有可能影響回轉(zhuǎn)窯的穩(wěn)定生產(chǎn),直接還原鐵的產(chǎn)率及回轉(zhuǎn)窯的利用系數(shù)也會受到影響。綜合來看,小型試驗中C/Fe質(zhì)量比在1.86-2.25為宜。
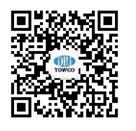
相關(guān)文章
[錯誤報告] [推薦] [收藏] [打印] [關(guān)閉] [返回頂部]