氫冶金的歷史、現(xiàn)狀以及我國的發(fā)展方向
2021-01-06 作者:佚名 網(wǎng)友評論 0 條
東北大學低碳鋼鐵前沿技術研究院
引言
在導致氣候變暖的各種溫室氣體中,CO2的貢獻率達一半以上,而人類活動排放的CO2有70%來自化石燃料,因此,各國都將交通運輸、冶金等行業(yè)采用氫氣代替CO的低碳能源取得技術突破作為一項主要抓手和目標。氫冶金是一種理想的綠色冶金工藝。發(fā)展氫冶金工藝是21世紀世界鋼鐵工業(yè)減排CO2工藝選擇的必然趨勢,而我國鋼鐵工業(yè)的產(chǎn)能占世界的一半,對于氫冶金工藝的需求比其它國家更為迫切。
1. 氫冶金技術起源和發(fā)展
1.1 HYL固定還原床裝置
最早的富氫HYL固定床還原裝置是40年代末建成的Maddras生產(chǎn)裝置。HYL反應罐法生產(chǎn)的入爐煤氣含H2 75%,CO 14%,CO2 8%,CH4 3%,H2/CO=5.36。后來發(fā)展成為連續(xù)生產(chǎn)的HYL-Ⅲ豎爐,其技術成熟,生產(chǎn)率高,目前已經(jīng)廣泛推廣應用,產(chǎn)能達到千萬噸。
1.2 H2-IRON氫冶金流化床工藝
該工藝的還原裝置為單管三段式還原沸騰流化床反應器,流化床中的鐵粉礦在2.75 MPa和540℃下還原,還原氣含H2 96%、N2 4%。該法使用天然氣或焦爐氣做原料,采用部分氧化法制取含H2 96%、N2 4%的還原氣。作業(yè)時,將小于20目的干礦粉用連續(xù)或間斷方式濃相輸送入三段還原流化床。各段床均設有還原氣體分布板,床段之間用帶閥門的管路連通,礦粉在三段還原流化還原床內(nèi)共停留45h,間斷操作。分別達到還原度為:第一段47%,第二段87%,第三段98%。為避免N2的循環(huán)積累,放出部分尾氣,再補充新H2后返回系統(tǒng)循環(huán)使用。
1.3 HIB高鐵團塊法(Nu-鐵法)
該法將天然氣與過熱蒸汽按蒸汽與甲烷3:1比例混合,送入重整轉(zhuǎn)化爐850℃下催化轉(zhuǎn)化,經(jīng)冷卻脫水后制成還原氣,重新將還原氣加熱到800℃,送入末段鼓泡流化床還原。還原氣含H2 85%~97%。經(jīng)300℃烘干、破碎、篩分處理后的小于10目的粉礦,用惰性氣體送入兩段干燥、預熱流化床。利用廢氣余熱和天然氣直接燃燒熱,在第一段預熱流化床內(nèi),礦石被加熱到315~350℃,除結(jié)晶水,然后在第二段預熱流化床將礦粉加熱到870℃。礦粉在第三段流化床被還原成FeO,在第四段還原床進行終還原。終還原流化床在0.2 MPa和700~750℃下完成還原。其產(chǎn)品成分為88.5% TFe,53.4% MFe,32.1% FeO,4.04%脈石,0.19% C,0.02% S。
1.4 FIOR氫氣流化床煉鐵工藝
FIOR法還原煤氣的H2/CO≥10,入爐氫氣溫度880℃,壓力1.05 MPa。FIOR法的操作指標為,礦石粒度-4.76 mm,其中-0.044 mm少于20%。產(chǎn)品TFe>92.4%,MFe 85%,C 0.7%,S 0.02%,(SiO2+Al2O3)3%。噸鐵耗天然氣4.0 Gkal,耗電180 kwh,耗水5.5 m3。
1.5 MIDREX天然氣基直接還原生產(chǎn)工藝
MIDREX豎爐的操作壓力為0.15-0.4 MPa,工藝煤氣中H2+CO≥90%,H2/CO=1.5-1.8,入爐溫度900℃。由于技術成熟,生產(chǎn)率高,MIDREX豎爐已經(jīng)廣泛推廣應用,已經(jīng)建成年產(chǎn)數(shù)千萬噸的產(chǎn)能,市場占有率穩(wěn)居世界第一。
1.6 中國科學院噸級間歇式氫氣流化床還原煉鐵
流化床還原試驗裝置為單管三段式還原鼓泡流化床,床層直徑600 mm,全高16.2 m,分上、中、下三段。試驗用-200目含鐵65%的釩鈦磁鐵礦做原料,日投料量2~8 t。試驗用化工富氫釋放氣做還原氣,還原氣入床廢氣經(jīng)一旋、溫度700~900℃,所得海綿鐵鐵粉的金屬化率>90%。床層氣流二旋、文氏管速度為0.48~0.58 m/s,洗滌塔煤氣放散率為90%。
1.7 廣東韶關5 t/d水煤氣豎爐海綿鐵試驗
豎爐采用無煙煤粉壓成柱狀煤條,加入內(nèi)徑1500 mm水煤氣發(fā)生爐通入氧氣燃燒制造凈化水煤氣,豎爐海綿日產(chǎn)量5噸以上,其CO+H2≥86%,H2≥48%,產(chǎn)品金屬化率>92%,S<0.08%,運行兩個月共進行了8次試驗,生產(chǎn)了海綿鐵760t。
1.8 成都5 m3豎爐還原攀枝花釩鈦磁鐵礦試驗
根據(jù)攀枝花釩鈦磁鐵礦氧化球團特點,還原氣的由天然氣與水蒸氣重整獲得,其CO+H2≥70%,CO/H2≥1.46,含N2 27%,入爐溫度>1150℃,爐頂煤氣溫度400℃,雖然試驗取得成功,由于天然氣資源缺乏,運行成本高,沒有推廣應用。
1.9 廣西間歇式沸騰流化床直接還原試驗
1980年,廣西流態(tài)化釩鈦磁鐵礦直接還原設計試驗組采用含氫70%的氫氮混合氣在廣西藤縣完成了間歇式沸騰流化床直接還原試驗,由于鐵礦粉中氧化鈦含量很高,其還原溫度達1000℃。
1.10 純氫氣豎爐還原理論
1980年美國鋼鐵協(xié)會主持下編寫和出版發(fā)行的專業(yè)文獻《直接還原鐵生產(chǎn)和應用的技術與經(jīng)濟》一書,該書的能量平衡圖表表明,純氫氣運行的豎爐和流化床直接還原流程的能耗很高。對于單段鐵礦粉流化床還原煉鐵,每噸金屬鐵循環(huán)的氫氣量需要4000 m3。對于逆流還原的豎爐法煉鐵,它用過的還原氣離開體爐料時具有高氧化度,每噸鐵循環(huán)的氫氣量為2500 m3。在確定直接還原工藝必需的能量時,需要考慮的主要因素有三個:豎爐總顯熱需要量(產(chǎn)品顯熱和廢氣顯熱,還原反應吸收的熱量Q,以及工藝熱損失);還原氣和還原物料的潛熱(LH);工藝生產(chǎn)還原氣所需的能量。過程所需的顯熱由預熱的鐵礦和還原氣來供給。
純氫氣豎爐還原的理論能耗幾乎是現(xiàn)代廣泛應用的HYL-III,或MIDREX直接還原鐵豎爐還原能耗的近3倍。1998年,在HYL-III豎爐專家來寶鋼交流時提到,豎爐不能用100%H2還原,一是還原氣全為H2,無碳源很難實現(xiàn)順行生產(chǎn);二是氫氣過輕,密度僅為CO的1/14,進入豎爐后就會迅速向爐頂逃逸,與混合氣體相比,氫氣在爐內(nèi)的路徑方向迅速改變。如果沒有與碳的相互變換和循環(huán)反應,沒有放熱的碳熱還原與強吸熱的氫氣還原溫度場的互補,氫氣在豎爐還原帶很難高效、低耗地完成還原鐵礦球團的任務。
1.11 FINMET粉礦流化床氫氣還原生產(chǎn)工藝
該工藝可直接用粒度小于12 mm的鐵粉礦為原料,粉礦被加熱到約100℃干燥過程在流化床內(nèi)完成。FINMET系統(tǒng)包括4個串聯(lián)的直徑4.5 m流化床反應器,彼此間通過氣體和固體輸送管路相連。粉礦在重力作用下由上至下運動,而還原氣體則以相反方向自下而上逆流通過。使用由天然氣與水蒸氣轉(zhuǎn)化產(chǎn)生的H2+CO2的混合煤氣與水蒸氣還原,4級流化床的操作壓力為1.1-1.3 MPa,最低位置流化床的入爐氫氣溫度850℃,最高位置反應器入口溫度約為550℃。入爐煤氣成分為H2/CO≥10,含H2≥85%。該工廠的特點是前端附設了一個高等級鐵精礦粉(TFe≥68%)精選車間,保證入爐粉礦原料含鐵均能夠達到68%以上,生產(chǎn)的HBI比重≥5 g/m3。
1.12 寶鋼BL法煤制氣-豎爐直接還原流程半工業(yè)試驗
BL法采用石球式加熱爐提升還原氣溫度,供豎爐生產(chǎn)直接還原鐵。經(jīng)過1998年6月、8月兩次共33天連續(xù)生產(chǎn)試驗,用山東兗州高硫煤(含63.9%C、3.96%S、20.1%Ash)及進口鐵礦球團等原料生產(chǎn)了132噸優(yōu)質(zhì)直接還原鐵(平均金屬化率為93.04%,含硫低于0.014%)。豎爐的還原溫度770-860℃,煤氣壓力0.1-0.4 MPa。豎爐還原帶平均工作容積利用系數(shù)達9.15 t/m³.d。試驗結(jié)果表明,扣除輸出煤氣,每噸直接還原鐵耗煤560kg,耗氧371 m³,同時副產(chǎn)硫磺12kg。這項首創(chuàng)的煤基氫冶金豎爐直接還原煉鐵法對煤種的適應性很廣,比其他煤基煉鐵法減少排放40%CO2、86%NOx,及81%SO2。試驗中無論將還原煤氣成分從德士古原始煤氣成分點H2/CO從0.85調(diào)整到Midrex豎爐還原氣成分點及達到HYL-Ⅲ豎爐還原氣成分點,均能長時間穩(wěn)定順行生產(chǎn)。
1.13 Circored工廠純氫還原
2001年魯奇冶金公司在特立尼達和多巴哥建成的年產(chǎn)能為50萬噸熱壓塊的Circored工廠用純氫氣作為唯一還原劑。采用兩級循環(huán)流化床反應器CFB和一個多級水平沸騰流化床FB反應器的串聯(lián)組合配置。氧化鐵粉礦首先在一個循環(huán)流化床中干燥預熱到850℃~900℃;輸送到一級預還原循環(huán)流化床反應器中,被0.4 MPa 750℃的氫氣還原30 min,達到75%預還原度;預還原粉礦再被輸送到一個操作壓力為0.4 MPa,氫氣溫度為650℃的二級終還原沸騰流化床還原反應器,爐料在此駐留時間長達240 min達到93%金屬化率。還原反應的吸熱由預熱粉礦和加熱循環(huán)的還原氫氣提供。最后,從二級沸騰流化床輸出的650℃直接還原鐵粉在快速加熱爐被加熱到700℃~715℃,加熱后的DRI粉輸送到排料系統(tǒng)。在排料系統(tǒng),N2取代H2,壓力降至大氣壓,然后熱壓塊機將還原鐵粉壓制出高密度熱壓塊HBI產(chǎn)品,熱壓塊過程的溫度至少達680℃。CFB預還原反應器出來的尾氣經(jīng)過熱交換器后進入多級旋風除塵器,收集的超細粉返回FB還原反應器;出口尾氣經(jīng)濕法除塵、降溫除去還原過程中產(chǎn)生的水,冷卻凈化的循環(huán)氫氣經(jīng)壓縮后加熱到750℃返回還原氣系統(tǒng)。使用純氫還原使爐頂煤氣凈化的工藝設備得到最大限度地簡化,使反應過程容易控制。Circored設備先進,能耗較高,工藝生產(chǎn)率不高,對操作維修人員素質(zhì)要求高,僅適合天然氣價格非常低廉的地區(qū)。
1.14 基于氫冶金的熔融還原煉鐵新工藝開發(fā)研究。
2006年-2011年,寶鋼、鋼鐵研究總院、上海大學開展“基于氫冶金的熔融還原煉鐵新工藝開發(fā):(1)粉礦流化床富氫煤氣預還原工藝;(2)冶金煤氣制富氫還原氣及其應用技術;(3)預還原粉狀DRI終還原工藝技術研究;(4)預還原粉礦還原集成技術;(5)粉煤壓型技術(6)終還原爐煤粉噴吹技術;集成上述單元技術研究,構(gòu)建使用粉煤和富氫還原粉礦的新工藝流程等。寶鋼研究院煉鐵所的初衷,是希望研發(fā)能夠?qū)OREX的爐料結(jié)構(gòu)由昂貴的球團礦改變?yōu)榈统杀镜姆鄣V為主,將大量輸出的COREX煤氣變換為富氫還原氣,采用氫冶金循環(huán)流化床技術將鐵礦粉預還原達到70%預還原度,壓塊后加入COREX預還原豎爐,預熱后入爐熔煉,取代原規(guī)劃建設的FINEX工藝。但因與Outotec公司談判引進其氫氣循環(huán)流化床中試設備時,因裝置規(guī)模發(fā)生分歧而放棄了流化床氫還原中試研究內(nèi)容。
1.15 國內(nèi)氫冶金氣基豎爐建設發(fā)展現(xiàn)狀
1999年徐匡迪院士在北京第125次香山科學會議上提出了鐵礦氫還原工藝設想,在上海2002年國家自然科學基金委員會再次提出應積極發(fā)展氫冶金。中晉太行建成世界首座年產(chǎn)30萬噸DRI的焦爐煤氣-豎爐生產(chǎn)裝置?;诮範t煤氣干重整技術,2020中晉太行山西冶金工程技術公司在世界上首次建成了年產(chǎn)使用焦爐煤氣的PERED工藝的氫氣豎爐直接還原鐵生產(chǎn)線,主體設備已經(jīng)建成,近期將開始試生產(chǎn)。河鋼集團宣鋼公司已經(jīng)完成使用焦爐煤氣、一期年產(chǎn)60萬噸DRI的HYL-ZR豎爐的初步設計。遼陽華信-東北大學、日照控股-鋼研總院等也在籌建氫冶金氣基豎爐直接還原生產(chǎn)線。
1.16 世界氫冶金發(fā)展趨勢
日本、歐盟等先進產(chǎn)鋼國均在研發(fā)氫冶金技術并規(guī)劃建設或策劃籌建以氫氣為還原氣的氣基豎爐直接還原鐵短流程產(chǎn)線。早期的氫冶金技術開發(fā)研究以及生產(chǎn)裝置均集中在南、北美洲之間天然氣價格十分廉價的國家。1990年以后,向富產(chǎn)天然氣的中東地區(qū)發(fā)展。為了減排CO2,現(xiàn)在在東亞及歐洲工業(yè)國家的氫冶金研發(fā)正在迅速開展,有可能后來居上。
2. 氫冶金技術的現(xiàn)狀
2.1 MIDREX直接還原生產(chǎn)工藝
2.1.1工藝流程簡介
美國表面燃燒公司從1936年開始研究天然氣基直接還原生產(chǎn)工藝,1966年成功突破天然氣重整制取還原氣和氣—固相逆流熱交換還原豎爐兩項關鍵技術。據(jù)2019年世界直接還原統(tǒng)計,氣基還原占75.8%,其中,Midrex法占60.5%,市場占有率一直世界領先。
Midrex流程適用于處理低硫礦石(S<0.01%)。還原氣以天然氣為原料時,在轉(zhuǎn)化爐中用大約三分之一爐頂氣除塵脫水后的CO2作氧化劑,與天然氣當量混合,然后送入裝有催化劑反應管的重整轉(zhuǎn)化爐。原料工藝氣在850-950℃轉(zhuǎn)化加熱爐中被鎳基催化劑催化發(fā)生重整反應,使其中的甲烷全部分解,控制煤氣中的H2/CO達到1.5-1.8,壓力為0.1-0.3 MPa,流量約為1800 Nm3/t產(chǎn)品。得到(H2+CO)>90%的還原氣。重整轉(zhuǎn)化反應式為:CO2+CH4=2CO+2H2,轉(zhuǎn)化后的還原氣直接送入豎爐使用。還原豎爐上部為預熱帶和還原帶,爐料通過下料管進入爐內(nèi),被熱還原氣預熱,進行還原反應。熱還原氣從豎爐中部周邊入口送入,經(jīng)還原反應后的煤氣從爐頂排出稱為爐頂煤氣。原料入爐后靠重力下行至豎爐底部即為成品排出,原料在豎爐中的下降速度(產(chǎn)量)由豎爐底部的排料機構(gòu)進行控制。豎爐還原帶高度約為9米時,原料在還原帶停留時間約5-6小時。入爐原料在預熱還原帶與上行的爐氣相接觸被預熱和還原,在固體狀態(tài)下還原成金屬鐵,金屬化率達92%。爐頂氣的溫度為400-450℃,壓力為0.05-0.20 MPa,含塵量為6000 mg/Nm3。還原后的海綿鐵在豎爐下部的冷卻帶被單獨循環(huán)的冷卻氣冷卻到50℃左右,海綿鐵經(jīng)過冷卻帶后含碳量約0.5-2.5%可按要求進行控制。冷卻氣入口溫度為40℃以下,壓力為0.1-0.3 MPa,流量約1000 Nm3/t產(chǎn)品,其成分為與爐頂煤氣接近,但是為了滲碳含有一定量CH4,冷卻氣離開豎爐的出口溫度約為450℃,含塵量為6000 mg/Nm3,經(jīng)過冷卻洗滌后溫度為35℃,含塵量為4 mg/Nm3,壓力約為0.05 MPa,加壓后循環(huán)使用。豎爐的進排料均采用氣體密封裝置,密封氣壓力為0.1-0.14 MPa,流量為1000-2000 m3/h,大致成分為:CO2 14.5%;H2O 20.3%;N2 64.2%;O2 1%。從豎爐排出的金屬化產(chǎn)品(52℃以下),經(jīng)皮帶運輸機輸送到鐵柵篩上(在皮帶上取樣和稱量)進行篩分,篩上的粘結(jié)塊經(jīng)破碎后與成品一起入成品倉。
MIDREX法豎爐在世界上迅速發(fā)展,已成為技術最成熟,生產(chǎn)量最大的直接還原煉鐵法。MIDREX豎爐第二代工藝使用一個高效熱回收裝置,充分利用了煙氣中的余熱換熱器依次對助燃空氣和工藝原料氣進行預熱,使用第二代轉(zhuǎn)化爐的MIDREX裝置綜合能量利用率,較第一代裝置約高出6.3%。MIDREX直接還原鐵豎爐具有以下優(yōu)勢:
(1)物料氣流逆流接觸,傳熱傳質(zhì)效率高;具有高作業(yè)率和高生產(chǎn)率;(2)頂煤氣循環(huán)利用,能源利用率高;(3)生產(chǎn)穩(wěn)定,沒有豎爐粘結(jié)問題,豎爐內(nèi)沒有死區(qū);(4)穩(wěn)定的料流和均勻的氣流分布創(chuàng)造產(chǎn)品穩(wěn)定的高金屬化率;(5)產(chǎn)品含碳量可以根據(jù)需求調(diào)整,提高煉鋼的作業(yè)效率;(6)煤制氣系統(tǒng)有脫硫工藝,產(chǎn)品含硫量非常低;(7)一代爐齡達10年以上,有些工廠設備已經(jīng)運行超過40年;(8)具有70多座MIDREX工廠的設計、生產(chǎn)運行經(jīng)驗,提供安全、高效、穩(wěn)定的工廠。
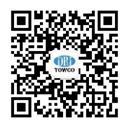
相關文章
[錯誤報告] [推薦] [收藏] [打印] [關閉] [返回頂部]