焦化廠剩余氨水蒸氨新工藝的應(yīng)用
作者:佚名發(fā)布時(shí)間:1970-01-01
劉俊倉(cāng) 劉運(yùn)龍(安陽(yáng)市恒威石化設(shè)備有限責(zé)任公司)
1 剩余氨水蒸氨新工藝
焦化廠的剩余氨水經(jīng)原料氨水槽靜止分離和陶瓷過(guò)濾等方式脫除焦油后;與蒸氨塔塔底部分蒸氨廢水進(jìn)行換熱后,送入蒸氨塔上段;用廢水循環(huán)泵將蒸氨塔底部分廢水,送入廢水加熱裝置,將廢水加熱到125~130℃后,返回蒸氨塔代替蒸汽。流程示意見(jiàn)圖(1)。
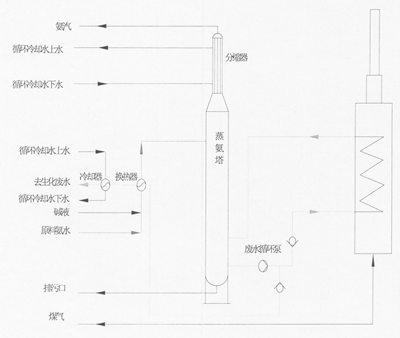
圖1 煤氣直接加熱蒸氨工藝流程示意圖
堿液經(jīng)流量計(jì)送入原料氨水泵壓出管中,以分解剩余氨水中的固定銨。蒸氨塔底的蒸氨廢水與原料氨水換熱,再經(jīng)冷卻器冷卻至40℃后,送至酚氰污水處理站。蒸氨塔頂?shù)陌逼?jīng)氨分縮器冷凝冷卻后,送入硫銨飽和器或煤氣脫硫裝置。表1列出了各種蒸氨工藝的指標(biāo)對(duì)比結(jié)果(以60萬(wàn)t/a)。
表 1 各種蒸氨工藝的指標(biāo)對(duì)比結(jié)果 (以60萬(wàn)噸焦炭/年)
項(xiàng)目 |
蒸汽直接蒸氨 |
蒸汽間接蒸氨 |
煤氣加熱蒸氨 |
導(dǎo)熱油加熱蒸氨 |
剩余氨水量,t/h |
15 |
15 |
15 |
15 |
蒸汽耗量,t/h |
3 |
3.8 |
0 |
0 |
廢水增加量,t/h |
3 |
0 |
0 |
0 |
電耗,kWh |
22 |
22 |
59 |
80 |
煤氣耗量,m3/h |
0 |
0 |
130 |
180 |
導(dǎo)熱油耗量,t/a |
0 |
0 |
0 |
2 |
年堿耗費(fèi)用,萬(wàn)元 |
108 |
108 |
108 |
108 |
噸水處理成本,元 |
42.10 |
43.27 |
14.04 |
17.13 |
投資,萬(wàn)元 |
200 |
230 |
350 |
420 |
折舊,萬(wàn)元 |
20 |
23 |
35 |
42 |
年操作費(fèi)用,萬(wàn)元 |
573.19 |
591.57 |
219.49 |
267.09 |
注: 1) 電力: 0.6元/kWh; 2) 蒸汽:120元/m3; 3) 煤氣:0.4元/m3 ; 4) 導(dǎo)熱油:4萬(wàn)元/t; 5)各種蒸氨工藝的循環(huán)冷卻水消耗量相同,未計(jì)入動(dòng)力消耗中; 6) 蒸汽間接蒸氨工藝未計(jì)冷凝水回收效益。
2 四種蒸氨工藝的特點(diǎn)
(1) 蒸汽直接蒸氨工藝。蒸汽直接進(jìn)入蒸氨塔作為蒸餾介質(zhì)加熱廢水的工藝簡(jiǎn)單,投資費(fèi)用少,但蒸汽用量大,造成生產(chǎn)成本高,并會(huì)增加蒸氨廢水量,增加了生化處理裝置的廢水負(fù)荷。
(2)蒸汽間接蒸氨工藝。蒸汽通過(guò)再沸器和廢水進(jìn)行熱量互換來(lái)加熱廢水,比蒸汽直接蒸氨工藝復(fù)雜,蒸汽消耗大,運(yùn)行費(fèi)用高,但其優(yōu)點(diǎn)是投資費(fèi)用較低,不會(huì)增加蒸氨廢水量。
(3)煤氣加熱裝置蒸氨工藝。用煤氣加熱裝置直接加熱廢水蒸氨的工藝流程短,生產(chǎn)穩(wěn)定,運(yùn)行費(fèi)用低,不會(huì)增加蒸氨廢水量。我公司在2008年10月為河南利源焦化公司(年產(chǎn)焦炭60萬(wàn)噸)建設(shè)了一套的焦?fàn)t煤氣直接加熱廢水的蒸氨裝置,各項(xiàng)操作指標(biāo)均達(dá)到了設(shè)計(jì)要求;運(yùn)行效果一直良好,用戶非常滿意,見(jiàn)圖2。另外,我公司在2008年還為河南誠(chéng)晨(120萬(wàn)噸)焦化公司設(shè)計(jì)的煤氣直接加熱廢水蒸氨項(xiàng)目的施工即將完成,不日即可投產(chǎn)。
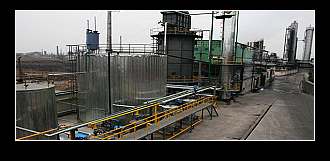
圖2 河南利源焦化廠煤氣直接加熱蒸氨裝置現(xiàn)場(chǎng)
(4)導(dǎo)熱油加熱蒸氨工藝。用煤氣加熱導(dǎo)熱油,再由導(dǎo)熱油加熱廢水;和煤氣直接加熱的蒸氨工藝相比,中間增加了一道工序,既增加設(shè)備投資費(fèi)用和熱損耗,又增加了導(dǎo)熱油的損耗和操作費(fèi)用,如出現(xiàn)導(dǎo)熱油泄漏,還會(huì)污染環(huán)境和增加安全隱患,流程示意圖見(jiàn)圖3。
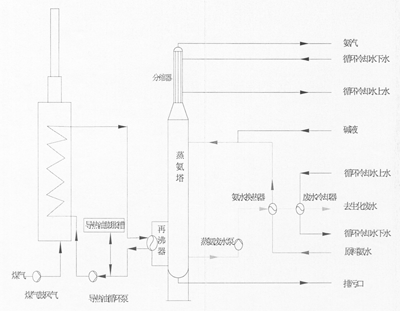
圖3 用導(dǎo)熱油加熱剩余氨水的蒸氨工藝
綜上所述,選擇煤氣加熱裝置蒸氨新工藝,特別適合于蒸汽供應(yīng)不足的焦化廠使用,半年即可收回成本,是節(jié)能、降耗、增效的有效途徑。